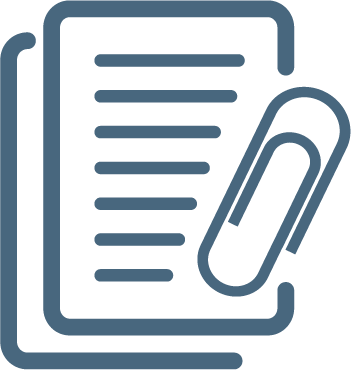
International Journal of Lean Six Sigma
SCIE-ISI SSCI-ISI SCOPUS (2010-2023)
2040-4166
2040-4174
Anh Quốc
Cơ quản chủ quản: Emerald Group Publishing Ltd.
SCIE-ISI SSCI-ISI SCOPUS (2010-2023)
2040-4166
2040-4174
Anh Quốc
Cơ quản chủ quản: Emerald Group Publishing Ltd.