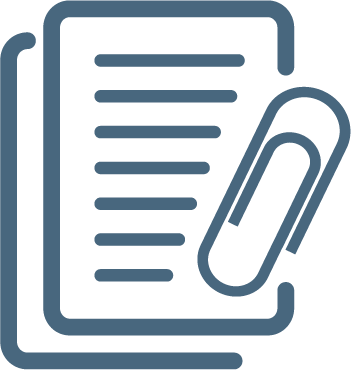
Integrating Materials and Manufacturing Innovation
SCOPUS (2012-2023)SCIE-ISI
2193-9772
2193-9764
Cơ quản chủ quản: Springer International Publishing AG , Springer Heidelberg
SCOPUS (2012-2023)SCIE-ISI
2193-9772
2193-9764
Cơ quản chủ quản: Springer International Publishing AG , Springer Heidelberg