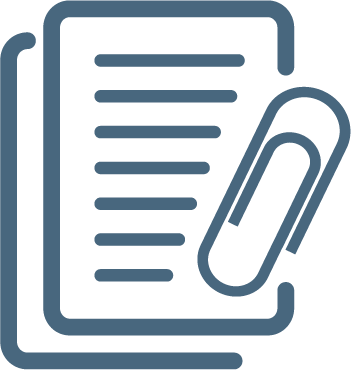
International Journal of Precision Engineering and Manufacturing
SCIE-ISI SCOPUS (2008-2023)
2005-4602
1229-8557
Cơ quản chủ quản: Korean Society of Precision Engineering , KOREAN SOC PRECISION ENG
SCIE-ISI SCOPUS (2008-2023)
2005-4602
1229-8557
Cơ quản chủ quản: Korean Society of Precision Engineering , KOREAN SOC PRECISION ENG