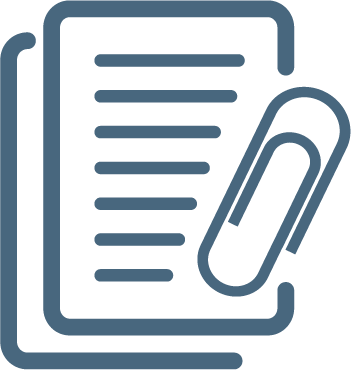
Journal of Turbomachinery
SCIE-ISI SCOPUS (1986-2023)
0889-504X
1528-8900
Mỹ
Cơ quản chủ quản: ASME , The American Society of Mechanical Engineers(ASME)
SCIE-ISI SCOPUS (1986-2023)
0889-504X
1528-8900
Mỹ
Cơ quản chủ quản: ASME , The American Society of Mechanical Engineers(ASME)