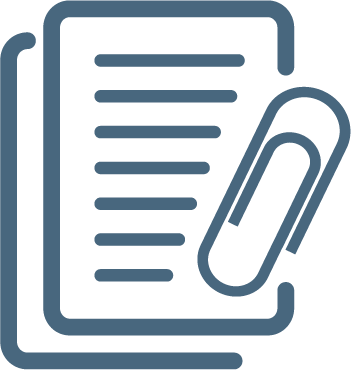
Industrial Robot
SCOPUS (1973-1989,1991,1993,1995-2023)SCIE-ISI
1758-5791
0143-991X
Anh Quốc
Cơ quản chủ quản: Emerald Group Publishing Ltd.
SCOPUS (1973-1989,1991,1993,1995-2023)SCIE-ISI
1758-5791
0143-991X
Anh Quốc
Cơ quản chủ quản: Emerald Group Publishing Ltd.