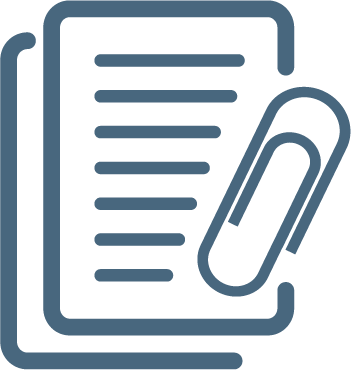
Welding in the World
SCIE-ISI SCOPUS (1969-1971,1973-2023)
1878-6669
0043-2288
Cơ quản chủ quản: Springer Verlag , Springer Heidelberg
SCIE-ISI SCOPUS (1969-1971,1973-2023)
1878-6669
0043-2288
Cơ quản chủ quản: Springer Verlag , Springer Heidelberg