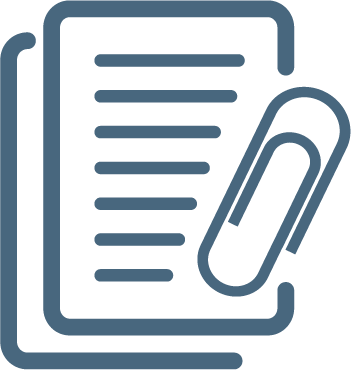
Forschung auf dem Gebiet des Ingenieurwesens A
SCOPUS (1930-1931,1964-2023)SCIE-ISI
1434-0860
0015-7899
Cơ quản chủ quản: Springer Verlag , Springer Heidelberg
SCOPUS (1930-1931,1964-2023)SCIE-ISI
1434-0860
0015-7899
Cơ quản chủ quản: Springer Verlag , Springer Heidelberg