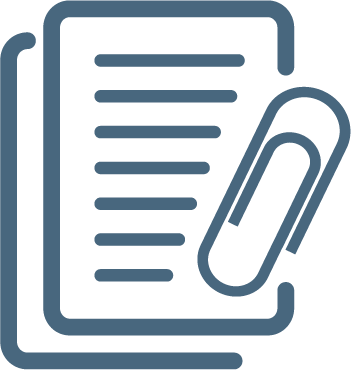
Fatigue and Fracture of Engineering Materials and Structures
SCIE-ISI SCOPUS (1979-2023)
8756-758X
1460-2695
Anh Quốc
Cơ quản chủ quản: WILEY , Wiley-Blackwell Publishing Ltd
SCIE-ISI SCOPUS (1979-2023)
8756-758X
1460-2695
Anh Quốc
Cơ quản chủ quản: WILEY , Wiley-Blackwell Publishing Ltd