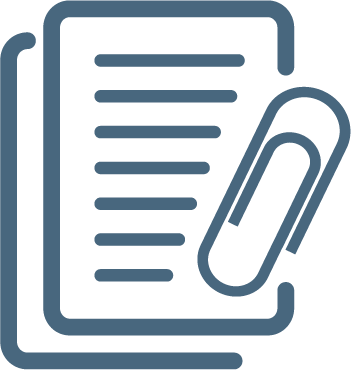
Metallurgical Transactions A
2379-0180
Cơ quản chủ quản: N/A
Lĩnh vực:
Các bài báo tiêu biểu
Correlation of microstructure with mechanical properties of 300m steel
- 1977
300M steel was subjected to a wide range of quenched and tempered heat treatments. The plane-strain fracture toughness and the tensile ultimate and yield strengths were evaluated. Results indicate that substantial improvement in toughness with no loss in strength can be accomplished in quenched and tempered steel by austenitizing at 1255 K (1800°F) or higher. Low fracture toughness in conventional...... hiện toàn bộ
Fundamental phenomena governing heat transfer during rolling
Tập 24 Số 6 - Trang 1307-1320 - 1993
To quantify the effect of roll chilling on the thermal history of a slab during hot rolling, tests were conducted at the Canada Center for Mineral and Energy Technology (CANMET) and at the University of British Columbia (UBC). In these tests, the surface and the interior temperatures of specimens were recorded during rolling using a data acquisition system. The corresponding heat-transfer coeffici...... hiện toàn bộ